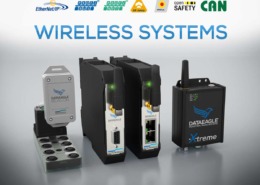
Here you find all about Control Technology.
Control Technology bei der Schildknecht AG
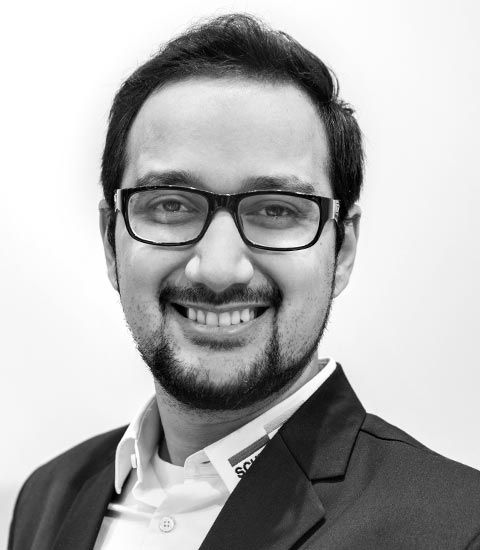
Zubair Khan
If you have any questions about our products, please do not hesitate to contact me.
If you have any questions about our products, please do not hesitate to contact me.
Depending on the choice of radio technology, a radio system can achieve a range of between a few metres and approx. 3 km. The line of sight and the antennas play a major role here. With DATAEAGLE radio systems, wireless PROFIBUS communication with (869MHZ (Europe) / 915 MHz (America) up to 3 km and with Bluetooth (worldwide usable) up to 1 km are possible.
Flexibility, networking in production, and smart interaction of machines and control systems – those are the ingredients of modern automation solutions. Plant operators use these solutions to identify and correct production variances faster than before, optimizing processes and reducing machine downtime, and thus increasing profitability. One of the key technologies of industrial automation is connectivity based on radio communication. You can integrate it in new plants and when doing refurbishments, as well as by retrofitting existing installations. As an alternative to cable-based data transfer, radio transfer secures maximum flexibility, not least in mobile and decentralized use cases. At the same time, it offers high data transfer reliability and security – if deployed correctly.
Today, many companies choose radio transmission to realize fieldbus communication with Profibus, Profinet or Profisafe. It proves effective in numerous industries and use cases – for instance in crane technology, water management, paper & pulp industries, lift and cableway installations, transportation and much more. In these automation technology implementations, for instance in process automation, radio technologies like Bluetooth, WLAN come into play – and soon 5G will be added to the mix. However, in some domains there are still reservations regarding reliability and stability of radio communication. These reservations are not entirely groundless, because when designing an automation solution, you need to consider the technical differences between cable and radio connections, to achieve similar robustness in data transfer.
Compared to cable-based solutions radio offers several advantages: from easy installation to the possibility of integrating complex networks with numerous slave applications and long distances, and profitability across the complete product life cycle (Blog article about alternatice data transmission solutions). However, not all radio data communication systems live up to the high standards of industrial use, regarding reliability and failsafe performance. This can lead to plant downtimes, reduced productivity and high costs – often even loss of confidence in the technology itself. Thus, it’s crucial to choose the optimal radio solution for interacting with the control communication of automation technology.
In cable-based connectivity between control units and I/O modules and standardized fieldbus systems like Profibus, Profinet and Canbus, telegrams are typically exchanged in millisecond cycles between sensors and actuators and the central control unit (PLC). Many fieldbus data transfers via radio connection replace a cabled solution with radio modules to transmit and receive data. But you must comply with the maximum response times defined by the bus communication, to be configured as application time in the PLC. If this response time is exceeded due to delayed or lost data packages, for instance caused by short interruptions like shadowing or other interferences from the surroundings, bus errors can occur. This leads to communication errors between control units and I/O modules, and at worst causing plant downtime.
Compared to cables, the challenge of wireless solutions is the available bandwidth. In general, data throughput via radio interface is lower than via cable. In addition to this, you need to factor in the increased latency due to “over-the-air” transmission. To secure robust and reliable data transfer via radio you therefore should choose intelligent radio systems especially designed to meet these requirements. What they’re doing is not just replacing cables with radio signals. They decouple the real-time interface from the wireless interface. Furthermore, they transmit pre-processed data packages and reduce the required bandwidth by not transmitting redundant data packages. In this way, radio paths are protected from overload, and fieldbus errors are avoided. This also means, that the real-time ability of the PLC and its maximum bus speed will remain unchanged. This results in optimal productivity and profitability of the production systems.
The patented DATAEAGLE technology from Schildknecht guarantees maximum reliability and safety for fieldbus data transfer via radio. The smart radio system analyses and pre-processes data packages before transmitting them. Sophisticated algorithms check redundancy and time stamps and decouple the fieldbus interface from the transmission time. This results in interference-free data transfer with minimal latency, improved real-time capabilities and significantly improved stability of data communication – even with short interruptions in the radio connection. Furthermore, you can configure the maximum length of downtime in which interference is filtered out automatically, and when actual interference should be reported to the PLC. The fieldbus protocol itself remains unchanged by this, and the safety monitoring time will not be compromised either. Thus, the system complies with the black-channel principle for safety use cases, like PROFIsafe and openSAFETY.
In this way system failures can be avoided. This saves time and costs related to troubleshooting and debugging, as well as productivity loss due to unplanned machine downtimes.
Schildknecht DATAEAGLE radio data systems replace cable-based solutions and other wireless technologies in numerous areas – whether they’re installed in a switching cabinet, or in direct use, indoor or outdoor, and under harsh surrounding conditions. All devices equipped with a Profibus, Profinet, CAN, Ethernet/IP or openSafety/UDP interface can be connected to these innovative wireless solutions. They provide a transmission range of up to 3 km and transfer speeds of up to 1,5 Mbit per second.
Easy top-hat rail mounting or placed directly on-site – these requirements were in focus during development of the solution, as well as fast and hassle-free installation. The devices behave transparently, just like a cable, so that the radio connection of your automation solution is connecting directly to the radio modules. A dedicated integration into the PLC or parameterization is not required.
At the same time, for all DATAEAGLE systems there are comprehensive tools available for monitoring and diagnostics of the radio path – directly on the device, locally in the control unit or for browser-based remote servicing.
Radio data systems with stabilized transmission are characterized by reliability and longevity without maintenance effort, by secure communication and resilience towards interference. Thus, they are ideally suited for use in automation technology. Furthermore, the patented DATAEAGLE product family offers maximum flexibility and easy plug & play installation. This will quickly and easily lead you to an optimal solution for wireless data transfer.
The black channel principle allows the transmission of safe and non-safe process data over the same network or bus line. Independent of the regular data transport mechanism used on this line, safety components can transmit data using an isolated safe protocol that tunnels through the underlying network channel. Since safe fieldbuses are pure application protocols without their own physical properties, the available bandwidths and cycle times depend on the data transport protocol used. Possible transmission errors are known and listed in the relevant standards IEC 61784-3 and IEC 61508.
What does this mean for PROFIsafe?
The PROFIsafe protocol has no repercussions on the standard bus protocols. It is intended to be as independent as possible of the respective transmission channel, whether copper cable, fibre optic cable, backplane bus or wireless. Neither the transmission rates nor the respective error detection play a role.
For PROFIsafe, the transmission channels are merely “black channels”. The DATAEAGLE 3732 and DATAEAGLE 4732 wireless PROFISAFE data radio systems were specially developed for the wireless transmission of PROFIsafe via Bluetooth. The use of the patented filter technology guarantees a stable, reliable radio connection, without bus errors in your PROFIsafe applications.